生产现场改善实例
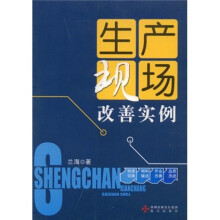
第一章 现场改善概论
1.1 现场改善的定义
1.1.1 改善定义
1.1.2 现场定义
1.1.3 现场改善
1.1.4 改善步骤
1.1.5 现场改善基本方法
1.2 现场改善的内容
1.2.1 生产线改善基础
1.2.2 作业改善原则
1.2.3 物料作业改善
1.2.4 接着接着式生产
1.2.5 生产布置优化
1.2.6 质量改善活动
1.2.7 生产维护改善
1.2.8 快速切换改善
1.2.9 现场5S改善
1.2.10 人机工程改善
第二章 生产线改善基础
2.1 生产线平衡
2.1.1 生产线平衡定义
2.1.2 线平衡改善
2.2 标准作业
2.2.1 标准作业的定义
2.2.2 实施标准作业的前提条件
2.2.3 制定标准作业的三要素
2.2.4 标准作业的作用
2.2.5 实施标准作业的步骤
2.2.6 作业指导书
第三章 作业改善基础
3.1 ECRS原则
3.1.1 E(Eliminate)取消
3.1.2 C(combine)合并
3.1.3 R(Reahange)重排
3.1.4 S(Simple)简化
3.2 动作经济原则
3.3 动素分析改善原则
3.4 MTM-2分析方法改善原则
3.5 MOD排时法动作改善原则
第四章 物料作业改善
4.1 物料搬运系统
4.1.1 物料原则
4.1.2 物料搬运系统原则
4.1.3 物料搬运方式
4.1.4 水蜘蛛作业整合系统
4.2 物料作业配置改善
4.2.1 重力送料装置
4.2.2 取消替代抓取
4.2.3 工具使用改善
4.2.4 物料专用道具
4.2.5 物料存放改善
4.2.6 自动供料改善
第五章 接着接着式生产线
5.1 什么是接着接着式生产
5.1.1 接着接着式生产的定义
5.1.2 接着接着式生产线的建立步骤
5.2 接着接着式生产线改善内容
5.2.1 作业改善
5.2.2 防错改善(Poka-Yoke)
5.2.3 自动送出(Hanedashi)
5.2.4 自恸化(Jidoka)
5.2.5 改善中的机械设计
第六章 生产布置优化
6.1 生产布置优化基础
6.1.1 生产布置优化的目的
6.1.2 生产布置原则
6.1.3 基本生产布置方式
6.2 系统布置计划
6.2.1 系统布置计划的定义
6.2.2 系统布置计划的步骤
6.3 单元式生产
6.3.1 什么是单元式生产
6.3.2 单元式生产的特点
6.3.3 一个流与批量生产
6.3.4 单元式生产线建立的要素
6.3.5 佳能的故事
第七章 质量改善活动
7.1 质量改善基础
7.1.1 质量管理三部曲
7.1.2 品质改善活动
7.2 质量改善的内容
7.2.1 改善作业区域清洁状况
7.2.2 改良机器和夹具的缺陷
7.2.3 消除控制各种变异因素
7.2.4 确保测量工具仪器准确
7.2.5 避免人员作业方法不当
7.2.6 改良产品零件设计缺陷
7.2.7 确保原材料质量的稳定
7.2.8 防错防呆的方法及装置
第八章 生产维护改善
8.1 TPM的定义和基本要素”
8.1.1 TPM的定义
8.1.2 TPM八大活动支柱
8.1.3 设备六大损失
8.1.4 MTBF和MTTR
8.1.5 一点通
8.2 生产维护改善内容
8.2.1 消除故障的潜在隐患
8.2.2 对设备零部件的改良
8.2.3 减少故障次数的改善
8.2.4 设备维护方法的改善
8.2.5 设备设计缺陷的改善
第九章 快速切换改善
9.1 快速切换的定义和作用
9.1.1 快速切换的定义
9.1.2 快速切换的作用
9.1.3 快速切换的特点
9.1.4 快速切换改善方法
9.2 快速切换的内容
9.2.1 事前充分准备
9.2.2 改善设备搬运
9.2.3 平行作业
9.2.4 通用化
9.2.5 道具替代工具
9.2.6 调整的标准化
9.2.7 改善切换方法
9.2.8 改善螺栓作业
第十章 现场5S改善
10.1 5S的定义和作用
10.1.1 5S的定义
10.1.2 5S的作用
10.2 整理(Seiri)
10.2.1 整理的作用
10.2.2 缺乏整理产生的浪费
10.2.3 整理的推行要领
10.2.4 区分必需和非必需物品
10.2.5 整理方法举例
10.3 整顿(Seiton)
10.3.1 整顿的作用
10.3.2 没有整顿产生的浪费
10.3.3 整顿的推行要领
10.3.4 整顿方法举例
10.4 清扫(Seiso)
10.4.1 清扫的作用
10.4.2 清扫的推行要领
10.4.3 清扫的重点
10.4.4 清扫方法举例
10.5 清洁(Seiketsu)
10.5.1 清洁的作用
10.5.2 清洁的推进要领
10.5.3 目视管理
10.6 素养(Shitsuke)
10.6.1 素养的作用
10.6.2 素养推行的要领
10.6.3 素养表现举例
第十一章 人讥工程改善
11.1 人机工程的定义和作用
11.1.1 人机工程的定义
11.1.2 人机工程的应用阻碍
11.2 人机工程改善内容
11.2.1 作业空间设计
11.2.2 工作台设计
11.2.3 座椅设计
11.2.4 手握式工具设计
11.2.5 微气候的设计
11.2.6 环境照明设计
11.2.7 噪声环境改善
11.2.8 振动的控制
11.2.9 减少空气污染
参考文献
1.1 现场改善的定义
1.1.1 改善定义
1.1.2 现场定义
1.1.3 现场改善
1.1.4 改善步骤
1.1.5 现场改善基本方法
1.2 现场改善的内容
1.2.1 生产线改善基础
1.2.2 作业改善原则
1.2.3 物料作业改善
1.2.4 接着接着式生产
1.2.5 生产布置优化
1.2.6 质量改善活动
1.2.7 生产维护改善
1.2.8 快速切换改善
1.2.9 现场5S改善
1.2.10 人机工程改善
第二章 生产线改善基础
2.1 生产线平衡
2.1.1 生产线平衡定义
2.1.2 线平衡改善
2.2 标准作业
2.2.1 标准作业的定义
2.2.2 实施标准作业的前提条件
2.2.3 制定标准作业的三要素
2.2.4 标准作业的作用
2.2.5 实施标准作业的步骤
2.2.6 作业指导书
第三章 作业改善基础
3.1 ECRS原则
3.1.1 E(Eliminate)取消
3.1.2 C(combine)合并
3.1.3 R(Reahange)重排
3.1.4 S(Simple)简化
3.2 动作经济原则
3.3 动素分析改善原则
3.4 MTM-2分析方法改善原则
3.5 MOD排时法动作改善原则
第四章 物料作业改善
4.1 物料搬运系统
4.1.1 物料原则
4.1.2 物料搬运系统原则
4.1.3 物料搬运方式
4.1.4 水蜘蛛作业整合系统
4.2 物料作业配置改善
4.2.1 重力送料装置
4.2.2 取消替代抓取
4.2.3 工具使用改善
4.2.4 物料专用道具
4.2.5 物料存放改善
4.2.6 自动供料改善
第五章 接着接着式生产线
5.1 什么是接着接着式生产
5.1.1 接着接着式生产的定义
5.1.2 接着接着式生产线的建立步骤
5.2 接着接着式生产线改善内容
5.2.1 作业改善
5.2.2 防错改善(Poka-Yoke)
5.2.3 自动送出(Hanedashi)
5.2.4 自恸化(Jidoka)
5.2.5 改善中的机械设计
第六章 生产布置优化
6.1 生产布置优化基础
6.1.1 生产布置优化的目的
6.1.2 生产布置原则
6.1.3 基本生产布置方式
6.2 系统布置计划
6.2.1 系统布置计划的定义
6.2.2 系统布置计划的步骤
6.3 单元式生产
6.3.1 什么是单元式生产
6.3.2 单元式生产的特点
6.3.3 一个流与批量生产
6.3.4 单元式生产线建立的要素
6.3.5 佳能的故事
第七章 质量改善活动
7.1 质量改善基础
7.1.1 质量管理三部曲
7.1.2 品质改善活动
7.2 质量改善的内容
7.2.1 改善作业区域清洁状况
7.2.2 改良机器和夹具的缺陷
7.2.3 消除控制各种变异因素
7.2.4 确保测量工具仪器准确
7.2.5 避免人员作业方法不当
7.2.6 改良产品零件设计缺陷
7.2.7 确保原材料质量的稳定
7.2.8 防错防呆的方法及装置
第八章 生产维护改善
8.1 TPM的定义和基本要素”
8.1.1 TPM的定义
8.1.2 TPM八大活动支柱
8.1.3 设备六大损失
8.1.4 MTBF和MTTR
8.1.5 一点通
8.2 生产维护改善内容
8.2.1 消除故障的潜在隐患
8.2.2 对设备零部件的改良
8.2.3 减少故障次数的改善
8.2.4 设备维护方法的改善
8.2.5 设备设计缺陷的改善
第九章 快速切换改善
9.1 快速切换的定义和作用
9.1.1 快速切换的定义
9.1.2 快速切换的作用
9.1.3 快速切换的特点
9.1.4 快速切换改善方法
9.2 快速切换的内容
9.2.1 事前充分准备
9.2.2 改善设备搬运
9.2.3 平行作业
9.2.4 通用化
9.2.5 道具替代工具
9.2.6 调整的标准化
9.2.7 改善切换方法
9.2.8 改善螺栓作业
第十章 现场5S改善
10.1 5S的定义和作用
10.1.1 5S的定义
10.1.2 5S的作用
10.2 整理(Seiri)
10.2.1 整理的作用
10.2.2 缺乏整理产生的浪费
10.2.3 整理的推行要领
10.2.4 区分必需和非必需物品
10.2.5 整理方法举例
10.3 整顿(Seiton)
10.3.1 整顿的作用
10.3.2 没有整顿产生的浪费
10.3.3 整顿的推行要领
10.3.4 整顿方法举例
10.4 清扫(Seiso)
10.4.1 清扫的作用
10.4.2 清扫的推行要领
10.4.3 清扫的重点
10.4.4 清扫方法举例
10.5 清洁(Seiketsu)
10.5.1 清洁的作用
10.5.2 清洁的推进要领
10.5.3 目视管理
10.6 素养(Shitsuke)
10.6.1 素养的作用
10.6.2 素养推行的要领
10.6.3 素养表现举例
第十一章 人讥工程改善
11.1 人机工程的定义和作用
11.1.1 人机工程的定义
11.1.2 人机工程的应用阻碍
11.2 人机工程改善内容
11.2.1 作业空间设计
11.2.2 工作台设计
11.2.3 座椅设计
11.2.4 手握式工具设计
11.2.5 微气候的设计
11.2.6 环境照明设计
11.2.7 噪声环境改善
11.2.8 振动的控制
11.2.9 减少空气污染
参考文献
《生产现场改善实例》其实就是作者的笔记,包括11个章节,以笔记的形式从不同的角度和层次来讲述如何进行现场改善,也记录了作者从事现场改善工作以来的学习、经历及见闻。本着“少谈点理论,多谈点实际”的精神,不讲过多的理论,只简单讲述改善的基本原则和基础方法,更多的是实际案例,并配合图片。
比价列表